Changing or adjusting molds in a Fully Automatic Block Making Machine involves a systematic process to ensure a smooth transition between different block designs or sizes.
Here’s a general overview of how molds are changed or adjusted in such machines:
- Machine Preparation:
- Before changing molds, the Fully Automatic Block Making Machine is brought to a complete stop, and the production process is halted. Ensure that the machine is powered off, and any remaining materials from the previous production run are cleared.
- Safety Checks:
- Perform safety checks to ensure that all components are in the proper position and that there are no residual materials or obstructions that could interfere with the mold change process. Follow safety protocols and use appropriate personal protective equipment.
- Access to Molds:
- Gain access to the mold or molds that need to be changed. This may involve opening doors, panels, or sections of the machine that provide access to the mold chamber.
- Release Pressure:
- If the mold is held in place by hydraulic pressure, release the pressure to allow for easy removal. This may involve activating a release mechanism or adjusting hydraulic controls to relieve pressure from the mold.
- Removal of Components:
- Remove any components that secure the mold in place. This may include bolts, clamps, or other fastening devices. Carefully follow the manufacturer’s instructions for dismantling and removing the mold.
- Lift or Slide Out the Mold:
- Depending on the machine design, the mold may be lifted or slid out of its position. Hydraulic or mechanical systems may be used to facilitate the movement. Fully Automatic Block Making Machine Ensure that the removal is done smoothly to avoid damage to the mold or the machine.
- Cleaning and Maintenance:
- While the mold is removed, take the opportunity to clean and inspect it. Remove any residue or debris from the previous production run. Perform routine maintenance checks on the mold components to ensure they are in good condition.
- Installation of New Mold:
- If changing to a different mold, install the new mold into the designated position. Align the mold correctly, making sure it fits securely. Use any fastening devices or clamps specified by the manufacturer to secure the new mold in place.
- Adjustment and Calibration:
- Fully Automatic Block Making Machines often have adjustable settings for different block sizes and designs. Adjust the machine settings and calibration to match the specifications of the new mold. This may involve setting the compression force, vibration intensity, and other parameters.
- Testing:
- Before resuming full production, perform a test run with the new mold to ensure that the machine is producing blocks of the desired quality and dimensions. Fully Automatic Block Making Machine in China Make any additional adjustments if necessary.
- Restarting Production:
- Once the new mold is successfully installed, adjusted, and tested, restart the Fully Automatic Block Making Machine to resume normal production operations.
- Documentation:
- Maintain accurate documentation of mold changes, including the type of mold used, production parameters, and any adjustments made. This documentation helps in tracking production history and troubleshooting potential issues.
It’s important to note that the specific steps for changing or adjusting molds can vary based on the design and features of the Fully Automatic Block Making Machine. Always refer to the manufacturer’s instructions and follow recommended procedures to ensure safe and efficient mold changes.
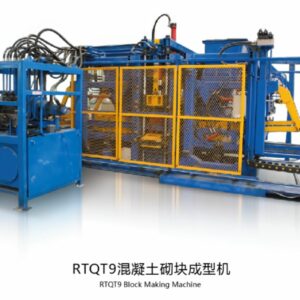