The widespread use of solar road studs in road safety and management offers several benefits, but it also comes with certain challenges. Here’s an overview of the advantages and potential drawbacks:
Benefits:
- Enhanced Visibility: Solar road studs significantly improve road visibility, especially at night and in adverse weather conditions. They provide clear visual cues to drivers, reducing the risk of accidents.
- Cost-Efficiency: Solar road studs are cost-effective in the long run because they utilize solar energy for illumination, reducing the need for external power sources and lowering energy costs.
- Sustainability: Solar road studs are eco-friendly as they harness renewable solar energy. They contribute to reducing the carbon footprint associated with road lighting and marking.
- Durability: High-quality solar road studs are built to withstand the rigors of road traffic and environmental conditions, offering long-term durability and minimal maintenance requirements.
- Flexibility: Solar road studs can be used in various applications, such as lane delineation, hazard warnings, speed control, and pedestrian safety. Their versatility makes them valuable tools for road management.
- Real-Time Information: Solar road studs with dynamic displays can convey real-time information to drivers, promoting safe navigation and traffic management.
- Safety in Work Zones: Solar road studs improve safety in construction and maintenance work zones by clearly marking boundaries, lane closures, and detours.
- Reduced Energy Consumption: Solar road studs with LED lighting consume less energy compared to traditional streetlights, contributing to energy conservation.
Challenges:
- Initial Installation Costs: The upfront cost of installing solar road studs, particularly in large quantities, can be a significant investment. However, the long-term cost savings may outweigh the initial expense.
- Maintenance: While solar road studs are relatively low-maintenance, they still require periodic cleaning, battery checks or replacements, and repairs. Neglecting maintenance can lead to reduced functionality.
- Durability in Extreme Conditions: Solar road studs must be designed to withstand extreme weather conditions, UV exposure, and the physical impact of vehicles. Inferior quality studs may deteriorate quickly.
- Vandalism and Theft: Solar road studs can be vulnerable to vandalism or theft, especially in urban areas. Security measures may be needed to protect them.
- Regulatory Compliance: There may be regulatory and safety standards that must be met, and adherence to these standards can add complexity to installation and maintenance.
- Adaptation to Existing Infrastructure: Retrofitting existing road infrastructure with solar road studs can be challenging, and it may require adjustments to accommodate the new technology.
- Interoperability: For systems that involve communication with vehicles or other infrastructure components, ensuring interoperability and standardization can be a complex issue.
- Battery Lifespan: The lifespan of the battery in solar road studs can affect their long-term performance. Batteries may need to be replaced periodically.
In summary, the benefits of widespread solar road stud use include improved road safety, sustainability, and cost-efficiency. However, challenges include initial installation costs, maintenance requirements, and the need to meet regulatory standards. Overcoming these challenges and utilizing high-quality solar road studs can result in safer, more sustainable, and efficient road management systems.
What are solar road studs, and how are they utilized in transportation and road safety?
Solar road studs, also known as solar road markers or solar cat’s eyes, are small, self-contained devices installed on road surfaces to enhance transportation and road safety. These devices utilize solar energy to power built-in LED lights, which make them highly visible, especially during nighttime and adverse weather conditions. Here’s how solar road studs work and how they are utilized in transportation and road safety:
How Solar Road Studs Work:
Solar road studs typically consist of the following key components:
- Solar Panel: Solar road studs are equipped with solar panels that capture sunlight during the day. These panels convert solar energy into electrical energy and store it in an onboard battery.
- LED Lights: Each solar road stud has one or more LED lights. These lights are typically energy-efficient and highly visible.
- Battery: An internal rechargeable battery stores the electrical energy generated by the solar panel. China solar road stud suppliers This energy is used to power the LED lights at night or during low-light conditions.
- Housing: The housing of the solar road stud is made from durable, weather-resistant materials. It is designed to protect the internal components from environmental factors and vehicle traffic.
Utilization in Transportation and Road Safety:
Solar road studs are employed in various ways to improve road safety, navigation, and traffic management:
- Lane Delineation: Solar road studs are often used to delineate lanes on highways and roads. By marking lane boundaries, they assist drivers in maintaining proper lane discipline and reducing lane departure accidents.
- Centerline Marking: On two-lane roads, solar road studs mark the centerline, preventing head-on collisions and ensuring safe driving at night or in low-light conditions.
- Curve and Intersection Warnings: Solar road studs are placed at curves, bends, and intersections to provide advanced warnings to drivers, enhancing their ability to navigate these areas safely.
- Speed Control: In certain areas, solar road studs may indicate changes in speed limits, prompting drivers to adjust their speed accordingly. This is often seen in school zones and construction zones.
- Crosswalks and Pedestrian Zones: In urban areas, solar road studs are used to mark crosswalks and pedestrian zones, improving pedestrian safety by making these areas more visible to drivers.
- Traffic Organization: Solar road studs contribute to organizing traffic by providing clear, consistent road markings. This promotes safe and orderly traffic flow.
- Work Zones: In construction and maintenance work zones, solar road studs are used to mark the boundaries of the work area, guide traffic through detours, and indicate lane closures.
- Visibility in Low-Light Conditions: Solar road studs are highly visible at night, in fog, rain, or snow. They enhance the visibility of road markings and provide continuous guidance to drivers.
- Dynamic Messaging: Some advanced solar road studs can display dynamic messages or symbols, conveying real-time information to drivers, such as lane closures or upcoming hazards.
Overall, solar road studs are valuable tools for road safety and management. They contribute to safer road navigation, enhanced visibility, and sustainable road infrastructure by harnessing solar energy to provide active illumination.
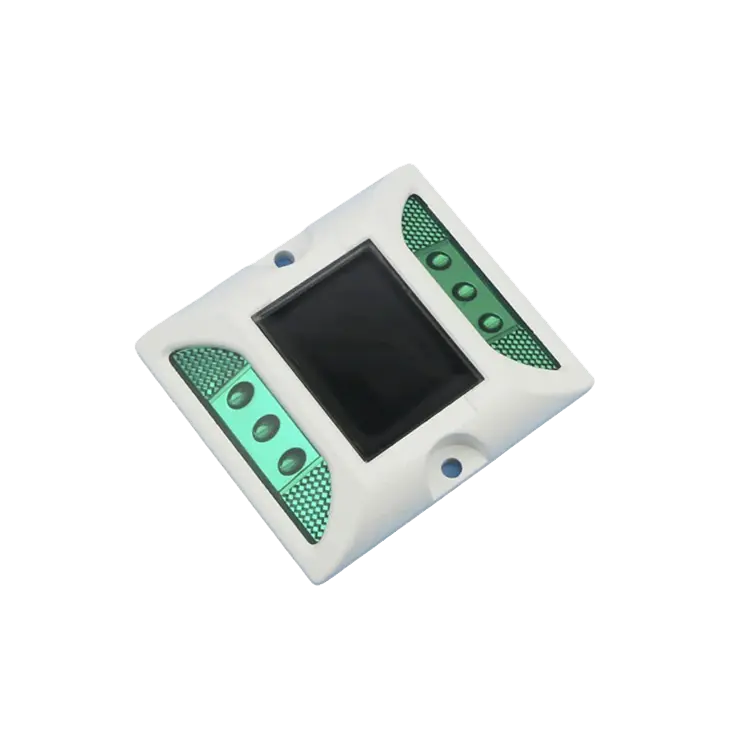