A block maker machine, also known as a block making machine or concrete block machine, is a device used to produce concrete blocks, which are commonly used in construction for building walls, pavements, and other structures. These machines automate the process of creating blocks, making it more efficient and consistent compared to manual methods. Here is an overview of a typical block maker machine:
Basic Components: A block maker machine consists of several key components, including a hopper, mixer, conveyor belt, block molds, and a hydraulic or mechanical system for compression and ejection of the blocks.
Hopper and Mixer: The hopper is where the raw materials such as cement, aggregates (such as sand or crushed stone), and water are loaded. The mixer combines these ingredients to form a homogenous mixture, ensuring that the concrete mix has the right consistency and strength.
Conveyor Belt: The conveyor belt transports the mixed concrete from the mixer to the block molds. It ensures a steady supply of concrete to the molds, enabling continuous block production.
Block Molds: The block molds are the key components that shape the concrete into specific block sizes and shapes. They are typically made of metal or plastic and come in various sizes, including molds for standard-sized concrete blocks, interlocking blocks, paving stones, and more.
Compression and Ejection System: Once the concrete is poured into the molds, a hydraulic or mechanical system applies pressure to compress the concrete and remove any air voids. This compression process helps to enhance the strength and density of the blocks. After the compression, the blocks are ejected from the molds using a mechanical or hydraulic system.
Control System: Modern block maker machines often come with a control system to automate and monitor the machine’s operation. The control system allows operators to adjust parameters such as block size, production speed, and the amount of raw materials used.
Block maker machines can vary in size, capacity, and automation level. Some machines are small and manually operated, suitable for small-scale projects or on-site production, while others are large, fully automated machines capable of producing a high volume of blocks per hour.
When selecting a block maker machine, blocks maker machine factors to consider include the required block sizes and shapes, production capacity, power source (electric, diesel, or hydraulic), ease of operation and maintenance, and the availability of spare parts and technical support.
It’s recommended to research and consult with manufacturers or suppliers to determine the most suitable block maker machine for your specific needs and budget.
Using a block maker machine for producing concrete blocks offers several advantages compared to manual methods. Here are some key advantages:
Increased Efficiency: Block maker machines automate the entire block production process, resulting in increased efficiency. These machines can produce a large number of blocks in a shorter period compared to manual methods. They eliminate the need for manual mixing, filling molds by hand, and manually compressing and ejecting blocks, saving significant time and labor.
Consistency and Quality: Block maker machines ensure consistent and uniform block production. The automated process ensures that the concrete mix is properly mixed and the blocks are consistently compressed to the desired density. This results in blocks of consistent size, shape, and strength, which is crucial for construction projects requiring standardized blocks.
Higher Production Capacity: Block maker machines have higher production capacities compared to manual methods. They can produce a large volume of blocks per hour, depending on the machine’s capacity and speed. This is particularly beneficial for large-scale construction projects that require a significant number of blocks within a specific timeframe.
Improved Block Strength: Block maker machines apply controlled and consistent pressure during the compression process, resulting in higher block strength. The machine can achieve greater compaction and reduce the presence of air voids, leading to stronger and more durable blocks. This is essential for ensuring the structural integrity and longevity of constructed walls, pavements, or other structures.
Flexibility in Block Design: Block maker machines offer flexibility in block design and customization. They can accommodate different block sizes, shapes, and patterns by simply changing the molds. This allows for creative options, such as producing interlocking blocks, decorative blocks, or blocks with specific surface textures.
Cost Savings: While the initial investment in a block maker machine may be higher compared to manual methods, it can result in long-term cost savings. The increased efficiency and productivity of the machine reduce labor costs and the time required for block production. Additionally, the consistent quality and strength of machine-produced blocks can minimize waste and rework, leading to cost savings in construction projects.
Improved Occupational Health and Safety: Using a block maker machine reduces the physical strain and repetitive tasks associated with manual block production. This improves the safety and well-being of workers by minimizing the risk of musculoskeletal injuries and other work-related health issues.
It’s important to note that the specific advantages of using a block maker machine can vary depending on the machine model, quality, and the expertise of the operator. Proper training, regular maintenance, and adherence to safety protocols are essential to maximize the benefits of using a block maker machine.
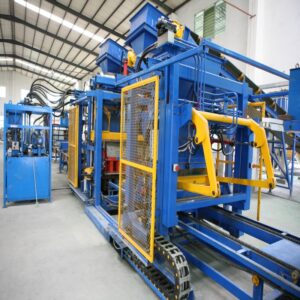